Should you require an operational review of your incinerator, one of our trained engineers can attend your site to re-commission your system. You engineer can tailor your incinerator settings to your needs, to ensure you’re optimizing the system as best you can.
Incinerator Service
Service Your Incinerator With Our Trained Engineers
Our highly skilled and proficient engineers will service your incinerator in line with manufacturer recommendations.
We also service many other makes. If your boiler is not on the list above please do still contact us as we are continually developing our in-house skills.
Why Myriad?
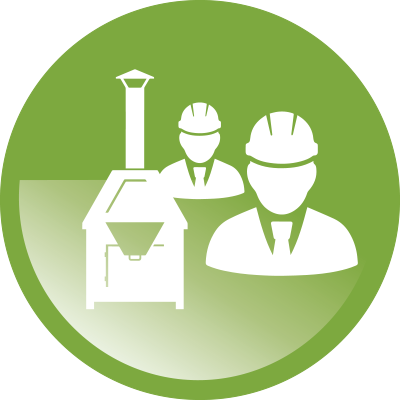
Waste Spectrum Incinerator trained engineers.
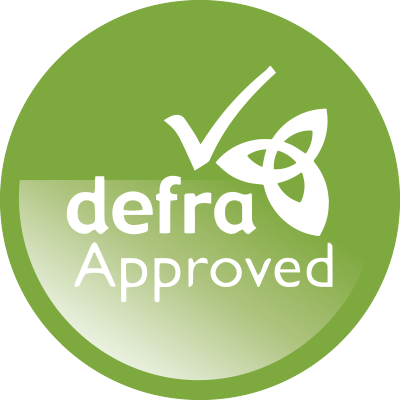
DEFRA compliant service in line with manufacturer recommendations.
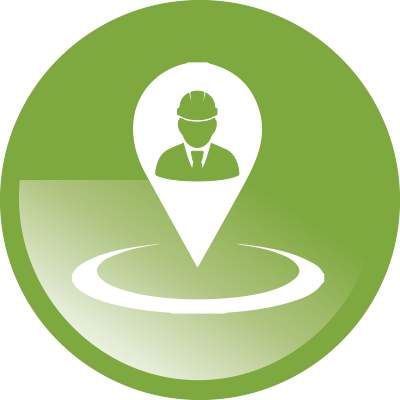
Locally based engineers.
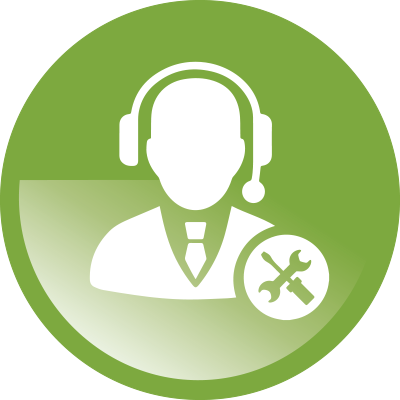
Dedicated service desk offering technical support and troubleshooting.
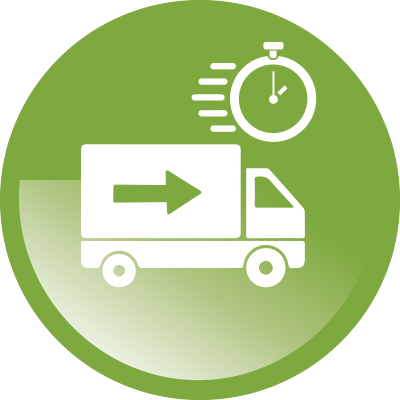
Exclusive UK distributor for Waste Spectrum parts with immediate despatch.
What's Included In Your Service?
- Removing of burners and thermocouples for inspection
- Inspection of rope seals and fibre lining
- Inspection of refractory concrete items
- Inspection of control panel.
- Full inspection of the incinerator – both inside and out.
- Starting of the machine and run up to temperature if required.
- Complete burner test to ensure this is in full working order.
- Replacement of necessary parts.
- Expert advice given on any replacements including full quote for follow up work.
.jpg?width=1500&height=1043&name=Volkan-450-cut-out%20(1).jpg)
Incinerator Service Package
From included travel costs to access to technical helpdesk support, Myriad will provide you with the following:
• Inc Service Burners: Re-set to approved settings
• Inc Check and re-set controls to correct settings
.png)
.png)
.png)
.png)
.png)
.png)
Additional Services
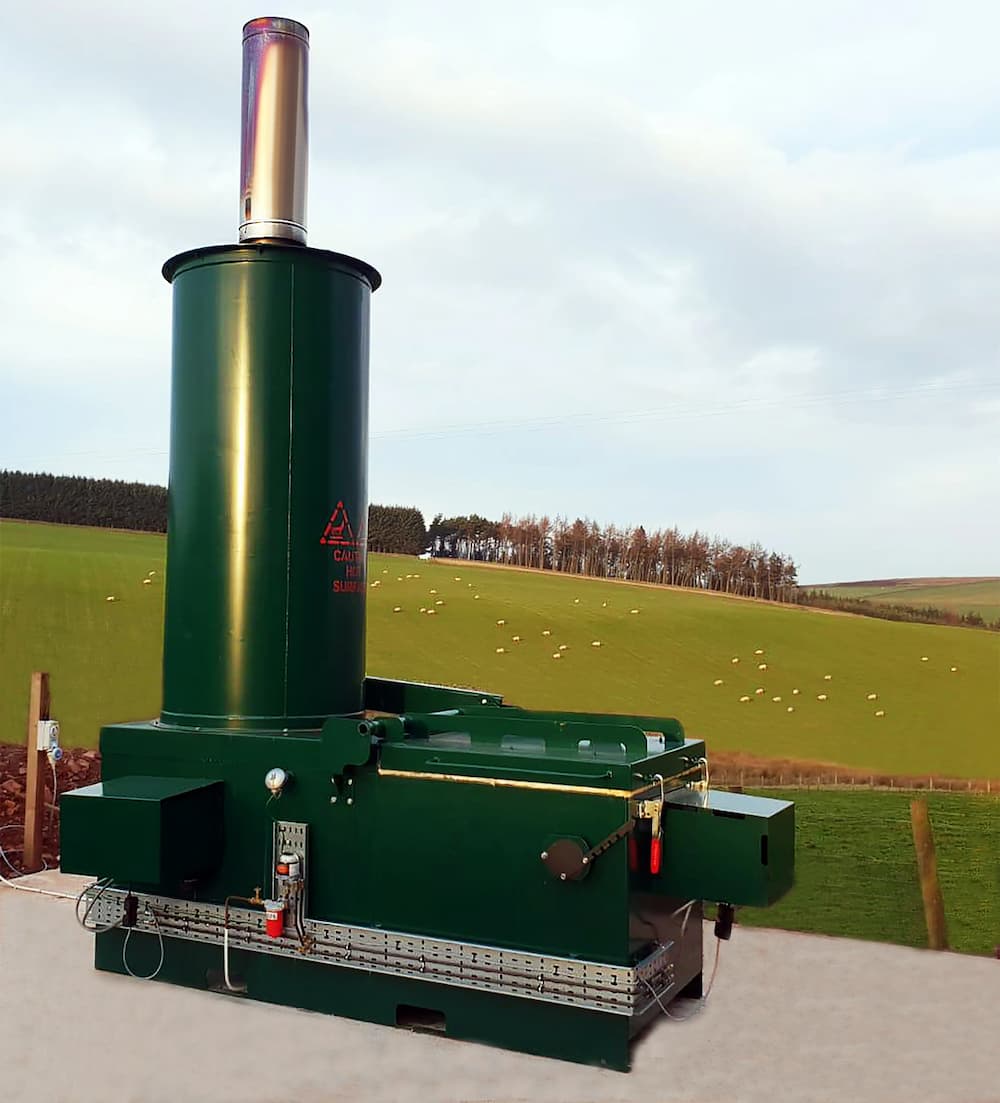
INCINERATOR COMMISSIONING
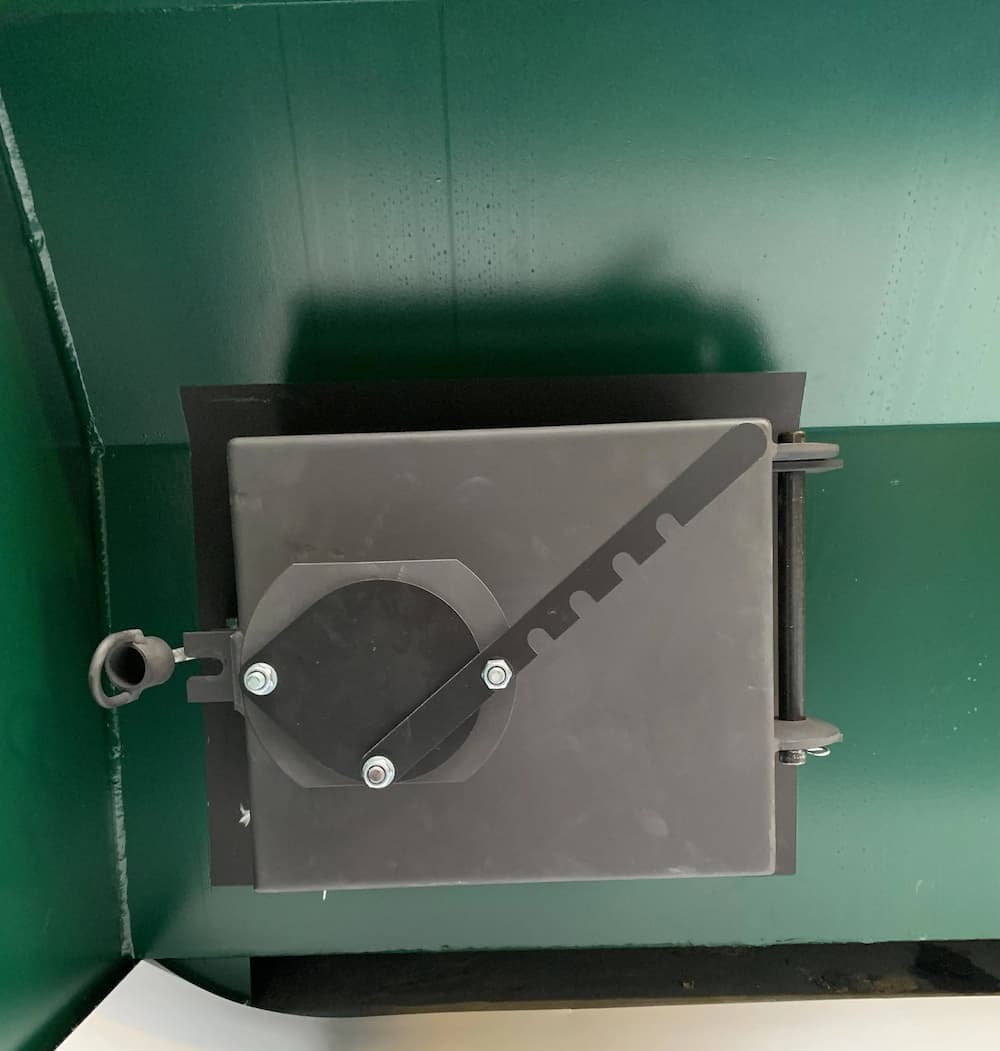
PARTS SUPPLY
We supply new parts for those in need of specific repairs and can refurbish burners. Please get in touch with us if you require a specific part to be replaced in your incinerator system. Many parts are available for same day despatch, and one of our trained engineers can also visit your site to fit this for you.
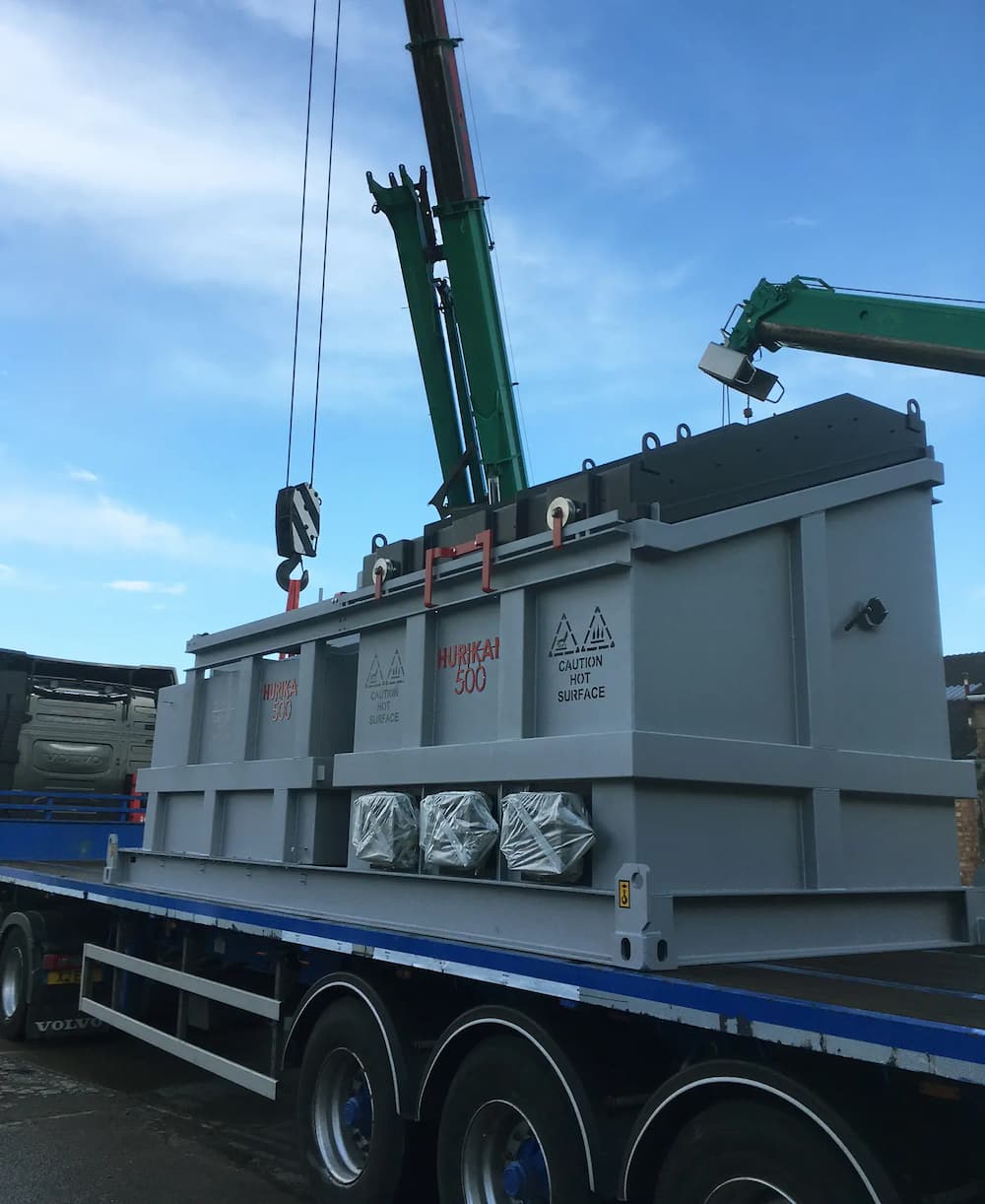
NEW/REPLACEMENT INCINERATORS
Is it time for a new incinerator? We are at your service for all new and replacement incinerator needs. From advice on the choosing right system for you to providing after-sell care, our experts are here for you.
Benefits Of Servicing With Myriad
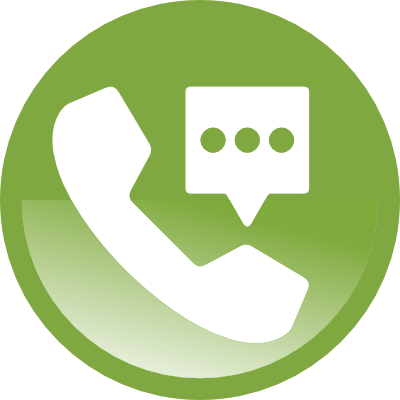
Technical Phone Support
Provides quick and expert advice over the phone, from one of our experienced technical engineers, to resolve incinerator issues without the need of a site visit.
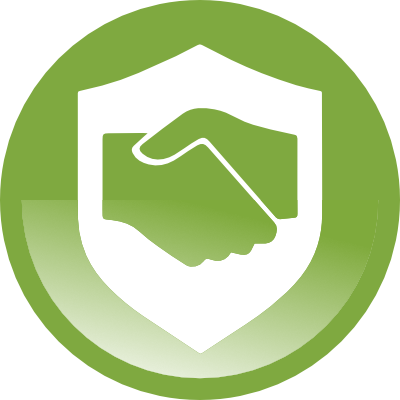
Reliability
Prevent issues with your incinerator by getting your system services with our reliable and friendly experts. Our proactive service can identify problems before they become bigger issues.
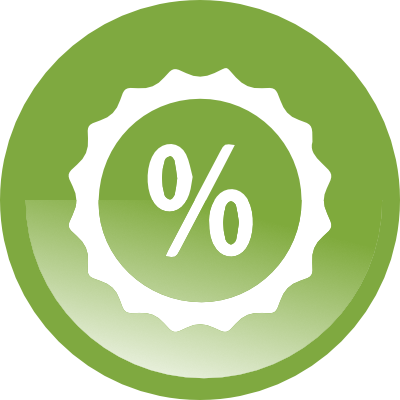
Spare Parts
We offer new equipment to those in need of parts for their incinerator, working closely with you from product choosing to product servicing.
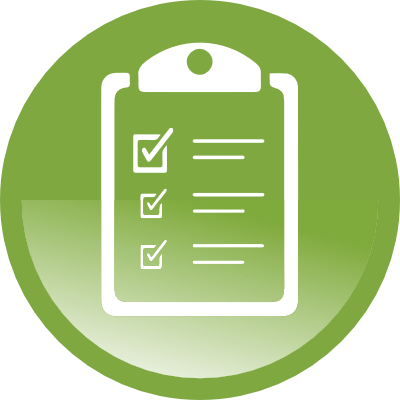
Priority Scheduling
Guarantee a convenient date for your service visit and benefit from priority appointments for call-out to have any issues sorted at the earliest opportunity.
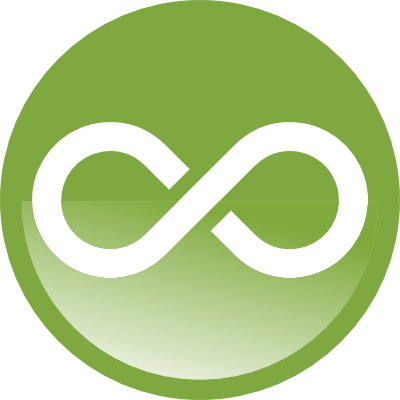
Longevity
We ensure your incinerator is working effectively as a waste solution for your site by pairing expert technicians with reliable machinery.
Additional Commercial Biomass Boiler Services
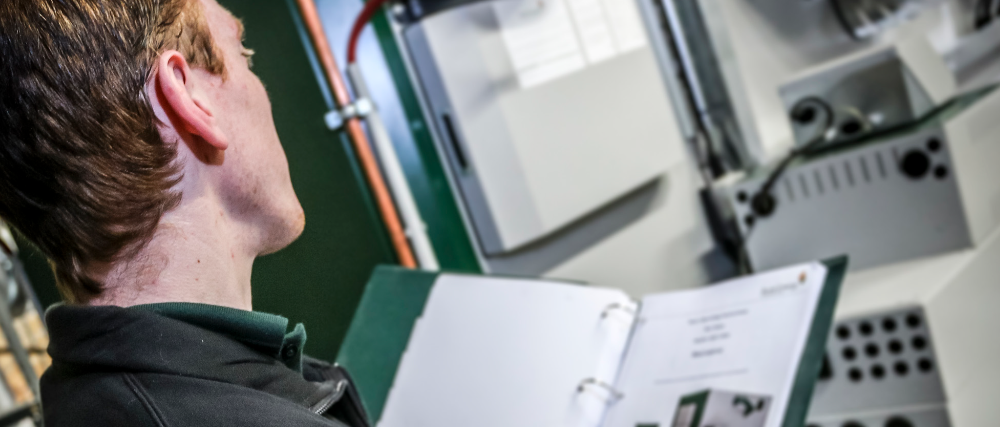
Boiler Combustion Optimisation
To guarantee your biomass system is operating efficiently, our engineers can check and amend the combustion parameters of your biomass boiler.
By cautiously running your biomass boiler up through each of the combustion phases, our skilled engineers will ensure your biomass boiler is achieving the most efficient and cleanest burn for your chosen wood fuel.
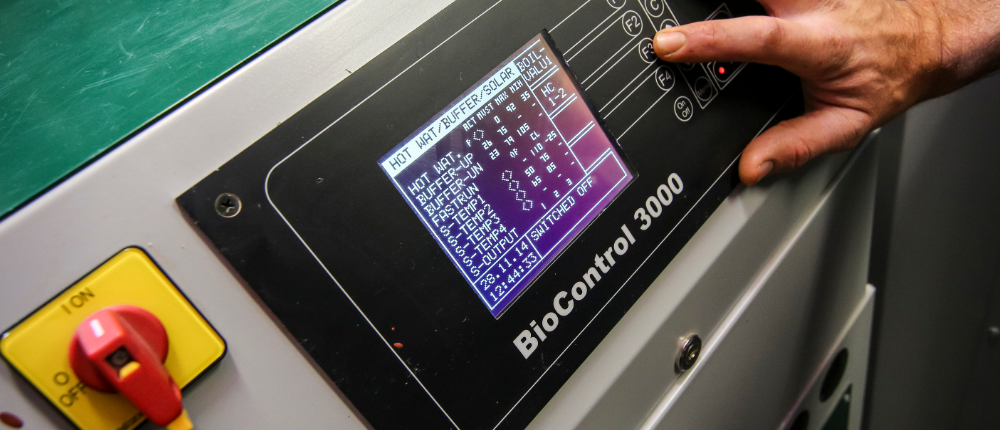
Boiler Commissioning
Should you require an operational review of your biomass boiler, or you are introducing new biomass fuel, one of our trained engineers can attend your site to re-commission your biomass boiler, selecting the most appropriate boiler parameters and combustion settings.
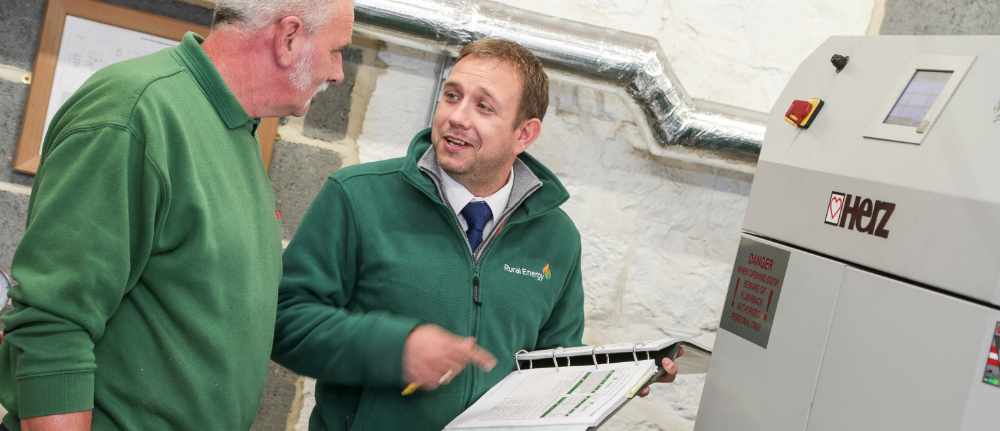
Additional Operator Training
Should a trained biomass operator leave your organisation, or you would like more trained biomass operators to look after your biomass system, we can provide specific onsite operator training.
Our training engineer can train up to 5 individuals at one time, and will demonstrate the general operation and navigation of the biomass boiler menu, explain the operating instructions and regular maintenance checks, and show how to quickly clear faults and restart the biomass boiler.
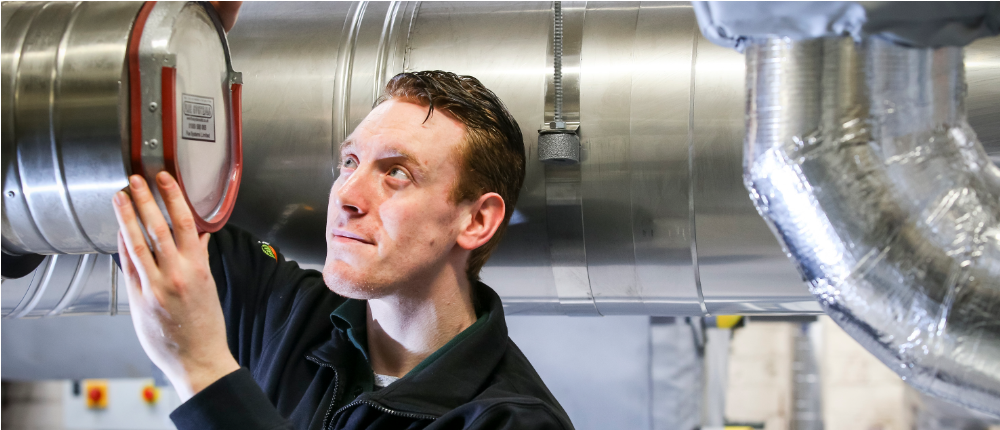
Condition & Operating Report
If you are unsure of the condition and operation of your biomass boiler, or if the boiler has been inactive for some time, we can thoroughly investigate your biomass system.
Our engineer will take photos, collate data, measure issues and find faults. If we can resolve any issues found on site, our engineers will undertake the works in the time remaining.
If additional parts or more time is required, our engineers will submit all data to our Head Office and compile a brief report. This report will include a recommendation of remedial actions required and all costs involved.
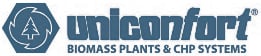
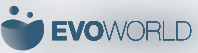

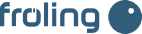
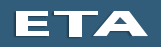